- Home
- >
- D-SIMCON
D-SIMCON
Unveiling the
essence of D-SIMCON
D-SIMCON is a suite of advanced domain-specific decision support modules for Capacity Planning & Optimisation, WIP Management and Scheduling & Dispatching in Semiconductor Manufacturing. The solution addresses the typical challenges in operating and managing the dynamic production line of a factory as complex as a wafer fabrication facility.
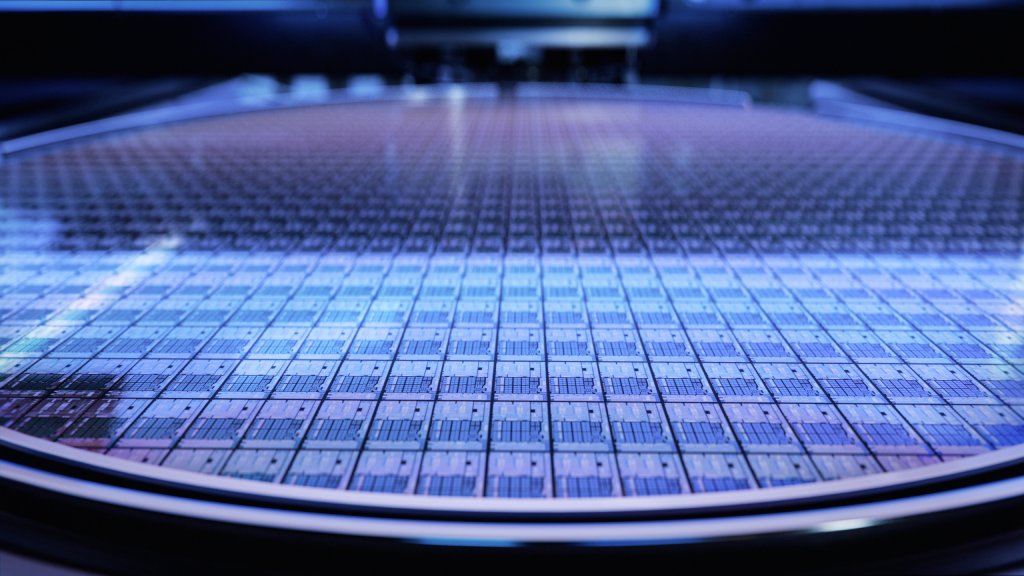
All modules can be deployed on a parallel computing infrastructure and are Cloud compliant to maximise scalability and minimise execution times.
Industry Challenges
Dynamic Business Environment
Everchanging external and internal business drivers – many of which are stochastic – call for proactive and agile planning and execution.
Complexity of Planning Parameters
Comprehensive tools for decision variable optimisation and action prioritisation in a resource-constrained production environment – with often non-intuitive interdependencies – are required.
Heterogenous Data Landscapes
Consistent and accurate data integrated from multiple sources without having to rely on simplistic assumptions is critical to decision-making.
Differentiators
Built for Semicon
Incorporating all pertinent domain-specific characteristics.
Unified Reporting
For performance monitoring and KPI forecasting.
Production Proven
Designed for immediate value creation.
Automated Model Generation
Users can focus on analysis and decision-making while models are automatically generated, calibrated and maintained.
Fully Integrated
One Digital Twin Framework built with independently deployable modules.
Highly Scalable
Seamless deployment and execution across small and large fabs.
AI-Enabled
Interface module to train large AI models.
Products
D-SIMCON
Function
Decision
Time Horizon
Strategic
Tactical
Operational
Day
Week
Month
Year